Efficient Product Recalls Management
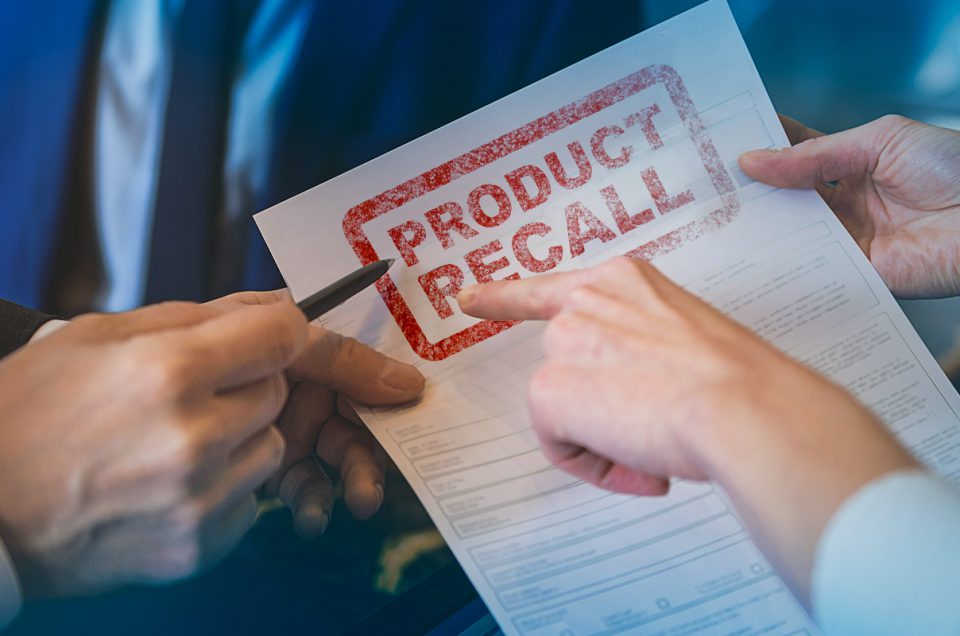
Product recalls: The Food Industry’s Biggest Threat to Profitability
A product recall can impact a manufacturer up to $10 million in direct costs, not to mention the cost of a damaged reputation. No manufacturer ever wants to face the prospect of a product recall, but it can and does happen. The product recall is a curative action that involves withdrawing from the market all products likely to present a defect that could affect the health or safety of consumers. The product recall scenarios are quite varied depending on the type of product, the type and scope of the supply chain and regulation the regulations that are in force. These scenarios also vary depending on the lifetime of the product, its manufacturing process and the actors involved in its life cycle.
Food recall is a fundamental tool in the management of risks in response to food safety events and emergencies. Due to the unforeseen nature of such incidents and the need to react quickly in the event of product recalls, one should be prepared in advance. The actions to be implemented to cope with this type of incident should be well defined beforehand. It is in this spirit that the authorities of some countries provide product recall guidelines.
How can traceability provide better product recalls management?
Traceability within food control systems is applied as a tool to control food hazards, provide reliable product information and guarantee product authenticity. Traceability and recalls are essential components of a national food control system. According to the ISO 22005 standard, traceability systems contribute to the search for the cause of nonconformity and enable, if necessary, withdraw and / or recall products (ISO, 2007).
By implementing traceability in warehouse management system, manufacturers could quickly pin-point a possible problem in the production process, determine where exactly the problem could have happened and why, find and recall all products that may be defective or contaminated.